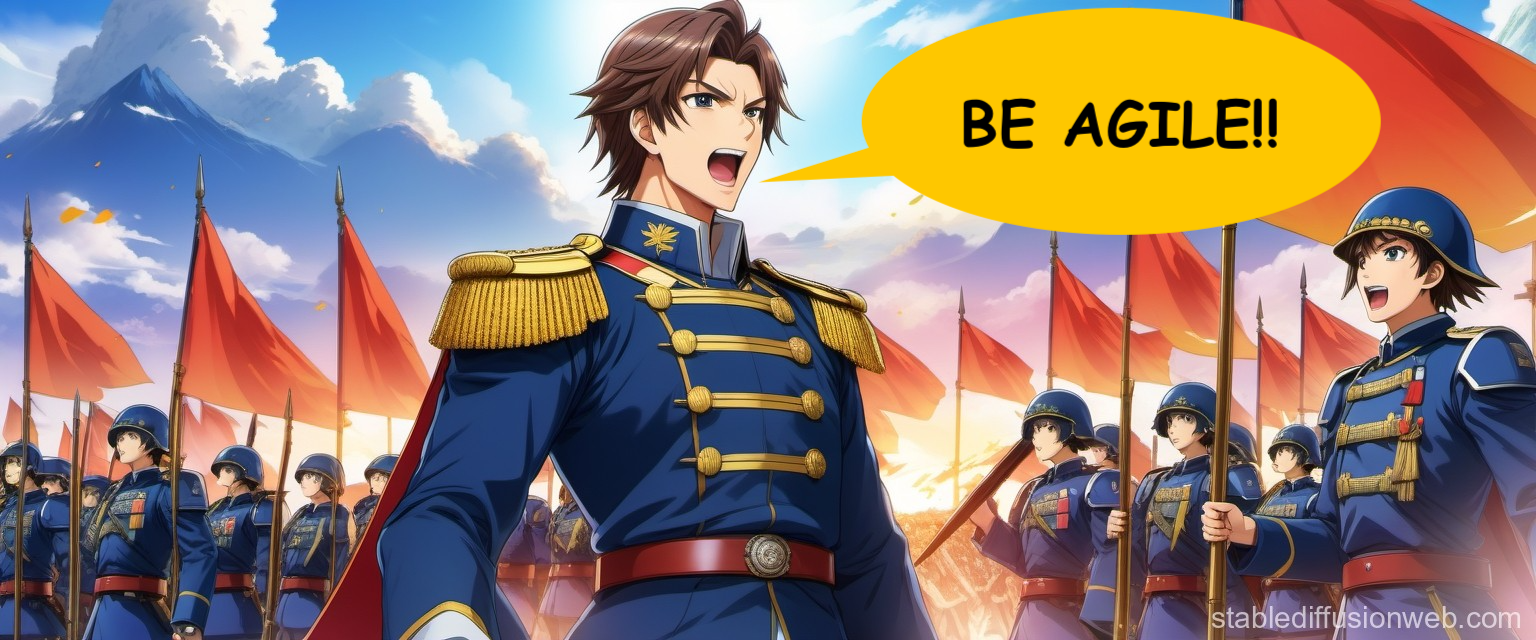
10 Signs of a Failing Lean-Agile Transformation
Have you ever had the feeling of “Is this really that agile everyone’s talking about?” when you are alone, after going through one or two years of transformation?
Many transformation efforts fall short. Unlike Dostoyevksy’s opening of Anna Karenina about unhappy families, failing transformations share some common signs. If you notice a few or more of the following signs, you might be on to something.
Before starting, here is a brilliant one from Comic Agile:

1. No impact
By far the most important indicator of a working lean agile transformation is creating impact. The meaning of impact would differ from organization to organization so the leadership should give answers that are right for them.
For this, an organization must have a clear understanding of what the success/improvement should look like. Missing tangible proof is a warning sign. You should get the feeling that things are improving compared to past quarters/years. If your perception is still at a level of “just another buzzword initiative” after some time, it’s problematic.
2. No measurements
One reason why most Lean-Agile transformations fail is the lack of proper measurements for impact indicators. Doing this part right is the most important -and often most skipped- step because it allows people to inspect the progress, have some reference to compare, stop doing things that don’t work, and try new approaches. Without this, it becomes like walking in a completely uncharted area blind.
Measuring wrong items (In software environments, examples can include measuring velocity, committed vs delivered, number of test cases “written”, amount of agile teams created, training/workshops conducted, etc…) is dangerous because it incentivizes wrong things and gives a false sense of improvement/change.
One must always stay skeptical about Lean-Agile transformation programs that don’t also integrate proper measurements that are directly related to things that concretely matter.
Some organizations may show resistance to the introduction of metrics, regardless of how appropriate they are. It means there is a bigger underlying problem, potentially in the conflict of interests category.
3. Focus on organizational changes rather than flow changes
Many transformations include renaming teams and hierarchies to squads, chapters, tribes, etc… Sometimes, it stops there.
As explained by Niels Pflaeging, Silke Hermann, and Brad Winn in this brilliant post, organization physics requires careful balancing of the three structures: Formal Structure, Informal Structure, and Value Creation Structure.
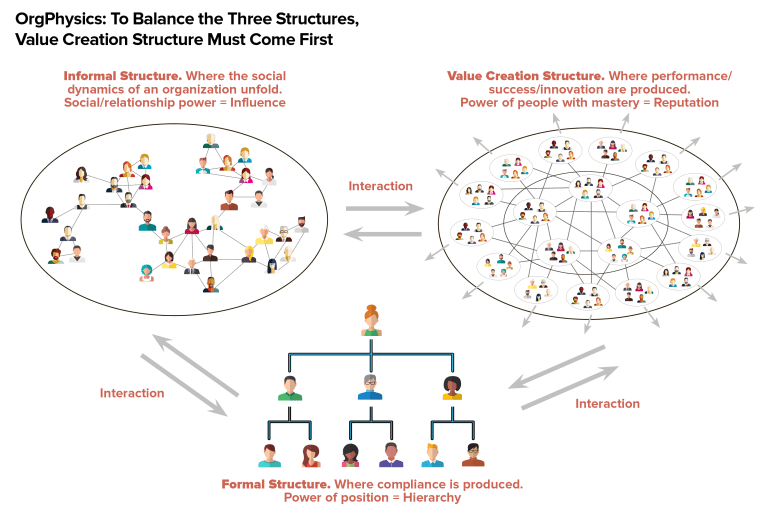
Image and Article Source: here
Silos are one of the biggest obstacles in flow efficiency. They incur handoffs and delays. They trap knowledge and experience inside and raise an organizational barrier to pass. Being a bottleneck becomes a justification for the existence of the silo, even a card to ask for more headcount. The argument that “Everybody needs us so we must be even bigger and more controlling” must be challenged.
I remember a highly siloed environment where teams were formed around technologies instead of products. There was linux team, database team, windows team, cloud team, containers team, and so on. As an engineer working on a product, you were supposed to constantly align or hand over work to those teams and wait for them.
After the transformation they all became squads. The higher level in the organization was renamed to tribe. But nothing concrete changed regarding how work is being done.
If changes done in the name of agile transformation stay limited to organizational reshuffles and labelings followed by intense meetings, kickoffs, and mandatory knowledge sessions instead of improving the effectiveness of the value creation structure, it will fail to deliver. It succeeds at one point, though: Keeping the old feudal power structure untouched.
In my experience, value creation structure is born naturally when the organization doesn’t raise more than the necessary organizational/process barriers. Likewise, keeping those barriers so high and rigid will ensure that value creation structure will not happen no matter what is thrown on the table in the name of transformation. You can’t force it to happen, you can only suppress elements that prevent it from happening and people will start creating the connections to get things done.
4. Focusing only on training on tactical methods while skipping principles and culture
It’s not uncommon to see management considering a Lean-Agile transformation as a matter of going through some training and applying playbooks.
Sometimes it’s leaders sending a copy of the Agile Manifesto to direct reports and ordering them to do that. Sometimes it’s C levels setting a goal for agile by defining a budget to spend on it in 1 year and expecting direct reports to finish the agile by the end of that year.
But this is not like changing office furniture. It’s a continuous cultural evolution that must always be supported and enabled by the top level by opening doors to reshape the organization, processes, and behaviors.
Culture change doesn’t happen like following instructions to build an IKEA cabinet.
While fundamental practical knowledge is essential, only internalizing the principles and changing the culture of the organization will make the change successful.
If the leadership keeps processes and structures effectively outside of the transformation (either deliberately or due to lack of basic knowledge) it won’t succeed.
5. Following recipes
It’s tempting to copy a successful company’s structure. After all, it’s proven to work. Countless companies tried to copy Toyota Production System (Which is the ancestor of Lean) or things that worked in other famous companies. To the leadership, copying sounds easy, cost-effective way of reaching the agility goal and then moving to the next project. You will notice this when other companies’ approaches are given targets to implement, rather than case studies to learn from their experience.
The leadership needs to understand that there’s no easy way of changing.
6. Leadership equating ‘agility’ with ‘speed’
Frequently leaders are heard saying “We have to be more agile, we must do things faster”. This is one of the biggest signs that indicate leadership either deliberately or naively has a very wrong understanding of the matter.
This creates a false expectation. Agility is a state of being that requires constant effort to stay at least there. It’s always uphill. Lean-Agile entities can do frequent course corrections with good feedback cycles to learn from results and do things differently/better. Continuously improving flow becomes the dna and speed becomes a byproduct of all of this.
7. Obsession with technology as the silver bullet
Agile means automating stuff and using modern tools: This is unfortunately what’s perceived when Lean-Agile is mentioned. It naturally leads to going crazy about adopting all the tools out there like crossing boxes on a bingo card, asking everyone to use more of them without first contemplating the processes and concrete needs. Difference between example Lean-Agile organizations isn’t caused by their tool adoption or usage rate. Using services and tools properly is just business as usual. It’s not a transformation.
The reason we see smart addition of tools in good Lean-Agile environments is that their principle, people, and value-driven environment ends up with decisions that involve using some tools for some tasks. Technology is a means to an end, not a goal. Skipping the whole journey and just shopping for technology isn’t a healthy shortcut for agility. There’s no shortcut to this.
8. No changes in processes and feedback loops
If the organization sees no need to change processes (regardless of a transformation) or establish better feedback loops, then transformation will fail.
Old, inefficient processes are amongst the biggest causes of delay in value streams. A working transformation should be causing revamps or removals of processes.
Feedback loops can involve many items. From escalations to analysis reports, from data points to expert opinions. People will want to give their feedback. But once the feeling of speaking towards the void settles, they will do it less and less. Without functioning feedback loops, it will not be possible to truly empower people who will actually make the change happen by bringing their domain expertise to different areas.
9. Ivory Tower deciding everything
The transformation must be owned, supported, and nurtured by the top level. Setting the expectation, and pointing to the north star are all challenging yet critical tasks to be done by the top level.
Sometimes it doesn’t stop there. The leadership continues further defining every single detail of the new operating model, leaving no area for actual domain experts. The more command-and-control driven the company is, the higher the risk of observing this. In most cases, this is accompanied by multiple signs in this list. Some can even consider this approach condescending.
10. Treating Lean-Agile transformation as a project
If the communication about the transformation often mentions it as a project, and tries to control it by the classic iron triangle (i.e. On-time, on budget, fixed scope), it’s already set up for failure. It’s common to see that the expectation is to finish the transformation in 1-2 years and be done with it, like changing printers in the office.
This indicates that the leadership has a completely wrong understanding. If consultants are guiding the whole journey, their competency or honesty to put the best interest of their customers can be questioned. When the leadership doesn’t understand, it will be impossible to improve.
Bonus: Not giving time and space for changes
With all the good intentions, if the leadership doesn’t allow people to prioritize this and instead expects them to work %100 business while squeezing the work on the transformation next to everything, it will have almost no chance of success. Given the limited time and cognitive energy, which is often fully consumed in environments that really need change, some things must be deprioritized so this work can be properly done.
Conclusion
We don’t know if there are better ways but so far, we haven’t found anything better yet We have more than half a century of proven experience and studies to draw lessons from. Still, many lean-agile initiatives fail. (Yet, it might still be sold as success in communication) The symptoms above would indicate serious deep problems in a Lean-Agile transformation effort. Root causes and potential solutions are completely different and very environment-specific matters.
If you are a leader nodding your head while reading the points above, it might be the time to ask different questions.